Selective Lazer Melting (SLM)
Selective Laser Melting or Metal Powder Bed Fusion is a 3D printing process which produces solid objects, using a thermal source to induce fusion between metal powder particles one layer at a time.
Most Powder Bed Fusion technologies employ mechanisms for adding powder as the object is being constructed, resulting in the final component being encased in the metal powder. The main variations in metal Powder Bed Fusion technologies come from the use of different energy sources; lasers or electron beams.
-
Types of 3D Printing Technology: Direct Metal Laser Sintering (DMLS); Selective Laser Melting (SLM); Electron Beam Melting (EBM).
-
Materials: Metal Powder: Aluminum, Stainless Steel, Titanium.
-
Dimensional Accuracy: ±0.1 mm.
-
Common Applications: Functional metal parts (aerospace and automotive); Medical; Dental.
-
Strengths: Strongest, functional parts; Complex geometries.
-
Weaknesses: Small build sizes; Highest price point of all technologies.
Selective Lazer Melting (SLM)
Selective Laser Melting or Metal Powder Bed Fusion is a 3D printing process which produces solid objects, using a thermal source to induce fusion between metal powder particles one layer at a time.
Most Powder Bed Fusion technologies employ mechanisms for adding powder as the object is being constructed, resulting in the final component being encased in the metal powder. The main variations in metal Powder Bed Fusion technologies come from the use of different energy sources; lasers or electron beams.
-
Types of 3D Printing Technology: Direct Metal Laser Sintering (DMLS); Selective Laser Melting (SLM); Electron Beam Melting (EBM).
-
Materials: Metal Powder: Aluminum, Stainless Steel, Titanium.
-
Dimensional Accuracy: ±0.1 mm.
-
Common Applications: Functional metal parts (aerospace and automotive); Medical; Dental.
-
Strengths: Strongest, functional parts; Complex geometries.
-
Weaknesses: Small build sizes; Highest price point of all technologies.
Selective Lazer Melting (SLM)
Selective Laser Melting or Metal Powder Bed Fusion is a 3D printing process which produces solid objects, using a thermal source to induce fusion between metal powder particles one layer at a time.
Most Powder Bed Fusion technologies employ mechanisms for adding powder as the object is being constructed, resulting in the final component being encased in the metal powder. The main variations in metal Powder Bed Fusion technologies come from the use of different energy sources; lasers or electron beams.
-
Types of 3D Printing Technology: Direct Metal Laser Sintering (DMLS); Selective Laser Melting (SLM); Electron Beam Melting (EBM).
-
Materials: Metal Powder: Aluminum, Stainless Steel, Titanium.
-
Dimensional Accuracy: ±0.1 mm.
-
Common Applications: Functional metal parts (aerospace and automotive); Medical; Dental.
-
Strengths: Strongest, functional parts; Complex geometries.
-
Weaknesses: Small build sizes; Highest price point of all technologies.
FORCYST is a mechanical engineering firm offering specialized professional engineering and design services in ASME pressure vessels, heat exchangers, piping systems and reviewing of calculations and drawings for these static equipment.
We provide engineering, consulting, design and drafting services of ASME pressure vessels and piping systems.
We are experienced in other pressure vessel related work such as:
1. Advanced custom configurations and components
2. Specialized process applications
3. Full range of pressure and service temperatures
4. Nozzle, flange, baffle, hatch and doors
5. TEMA Heat Exchangers
6. API storage tanks
7. Rectangular tanks, bins, foundations and support systems
We base our ASME code calculations on the most accepted commercial software programs with unusual details calculated by Spreadsheet to provide the calculations required to solve your design problems.
DESIGN TOOLS
These educational Excel spreadsheets can get your project started in the right direction.
Calculations are included for Shells, Heads, Nozzles and even the flat layout of a cone.
Whatever the project, FORCYST enhances its own professional expertise with the power of partnership to meet each client's expectations. Our desire is to create, not only superior engineering output, but also a strong and lasting client relationships.
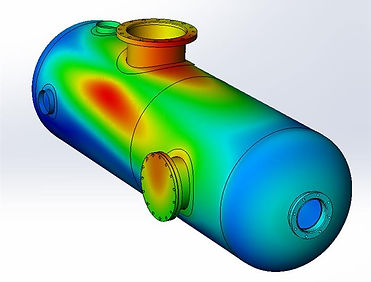